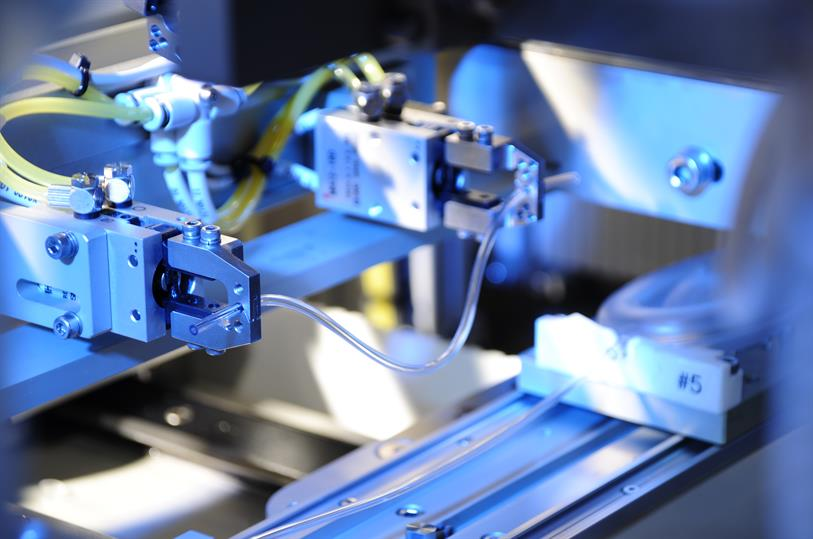
If you’re bringing new goods to the market, one of the most important steps is product testing. Testing tells you how much force individual parts can take, but that is only the beginning. It also helps you document the safe operating conditions for your goods, allowing you to provide better customer support. It can also provide you with insight into failure conditions and to ensure they do not fall under regular use conditions. Through methods like destructive testing, you can gain the knowledge needed to safely roll out virtually any product, from consumer and household goods to professional equipment aimed at the B2B market.
Create a Maintenance Plan for Your Customers
One of the most important documents you can provide in an owner’s manual to a new machine is the maintenance plan. If you are building with metal parts, stress tests and other product testing methods provide you with the information you need to understand when your products need new parts or preventive maintenance. This data can then be used to write up a set of procedures for customers, providing them with the instructions they need to get the most out of an investment into your product. If your product has a warranty, requiring the recommended maintenance plan be followed is quite common as a cost-saving measure that preserves your relationship with customers.
Limit Liability
If testing shows any major issues with the product, you have an opportunity to redesign features until the customer experience aligns with your expectations. That helps you avoid liability for products that fail due to poor design or material quality by making sure none of the regular and recommended use conditions for your product result in failure. Without robust testing, you take a big risk with every product that hits the market. The more severe the consequences of a mechanical failure, the more important it is to test your goods.